Pride & Craftmanship
A commitment to excellence drives every aspect of our work. Meticulously crafted, each coil winding solution embodies our commitment to quality and reliability. With a focus on innovation and attention to detail, we deliver products that enhance your production capabilities and stand the test of time.
Fundamentals of Coil Winding
Coil winding is a critical process used in various industries, particularly in the manufacturing of electrical components such as transformers, motors, inductors, and electromagnets. In this application, conductive wire, typically made of copper or aluminum, is wound around a core or bobbin in precise patterns to create an electromagnetic field when electrical current flows through the wire. The number of turns, wire gauge, tension, and winding configuration are key parameters that influence the electrical properties of the finished coil, such as inductance, resistance, and current capacity. The process of coil winding can be automated or done manually, depending on the complexity of the design and the required precision. Automated coil winding machines are commonly used for high-volume production, ensuring tight control over the wire placement, tension, and speed, which is essential for achieving consistent electrical performance and minimizing defects.
In applications such as transformers, the winding must be carefully insulated to prevent short circuits, and different layers of windings may be used to meet specific design requirements. In motor manufacturing, coil winding is crucial for creating the magnetic fields that enable rotation. Similarly, in inductors and electromagnets, coil winding determines the strength and efficiency of the magnetic field produced. Coil winding plays a pivotal role in achieving high efficiency, reliability, and performance in electrical systems, making it a fundamental process in modern electronics and electromechanical applications.
Quality Manufacturing
Our rigorous inspections, tests, and focus on design and manufacturing have established industry-leading quality standards.
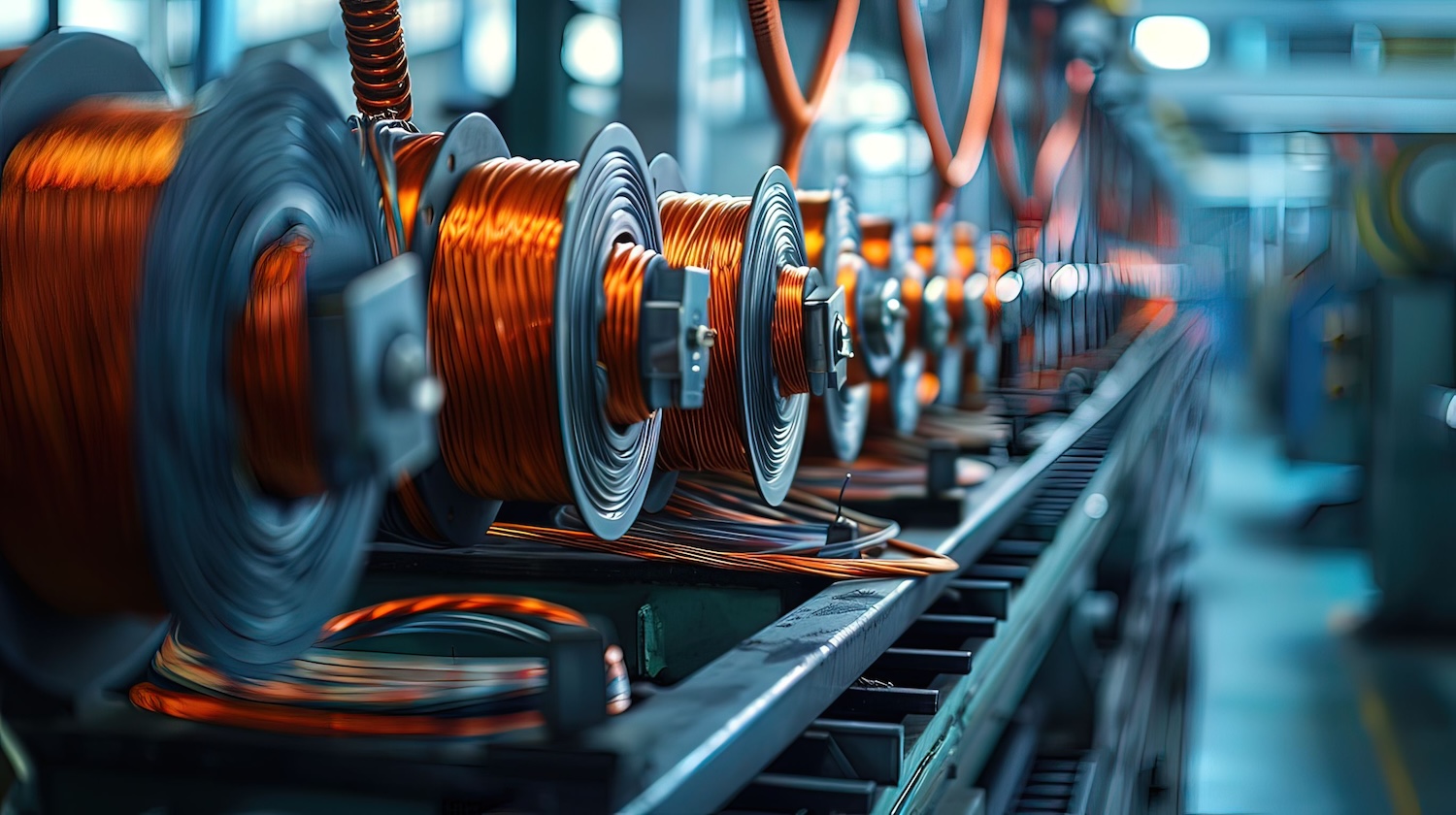
Scalable Applications
- Armatures
- Heating Elements
- Field Coils
- Catheter Guide Wires
Tradition & Technology
Our unique blend of tradition and technology offers durability and cutting-edge production capabilities. Since 1943, our focus has been maximizing your coil winding production for efficiency and quality.
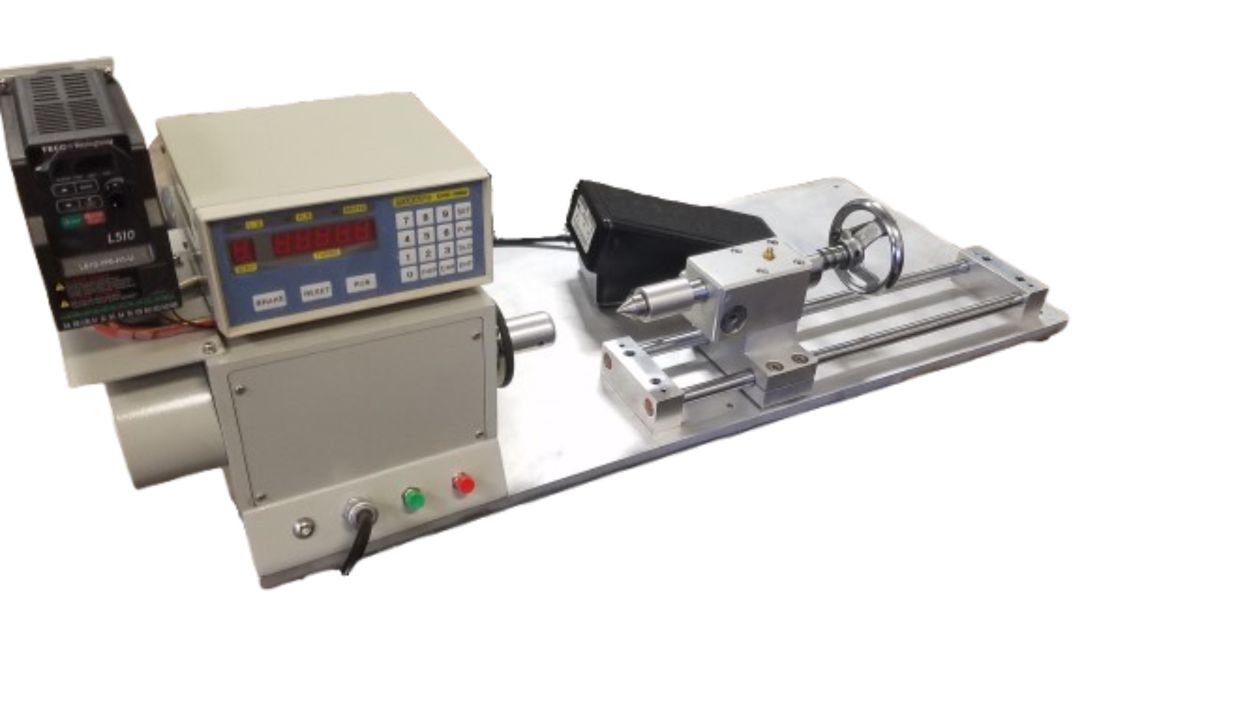
GS-F60BFT – Low cost, General use, 40-18AWG
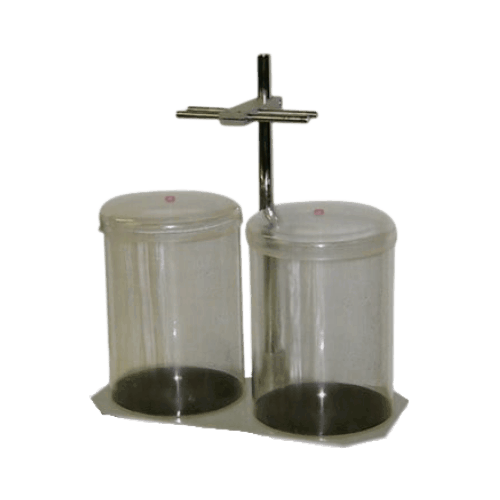
GSM-B2 – De-Reeler Base
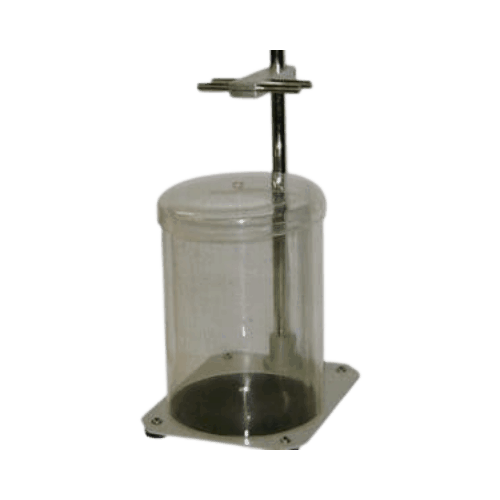
GSM-B1 – De-Reeler Base
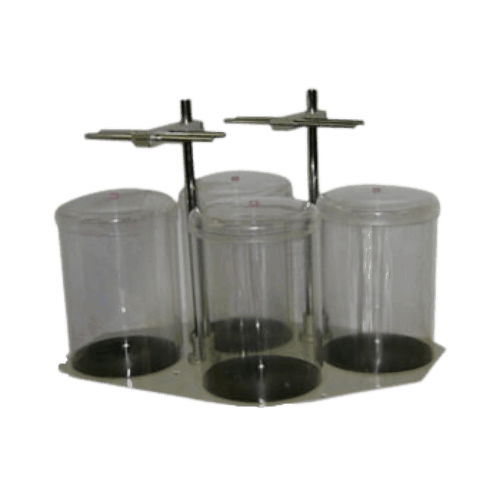
GSM-B4 – De-Reeler Base
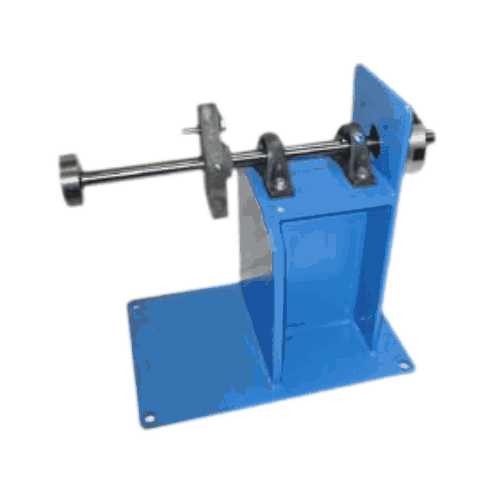
Heavy Duty Tension – T-153 Series
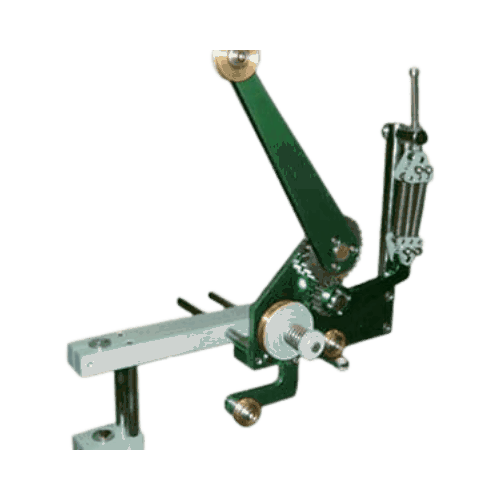
GSM-L02 – Tensioner Head 20-12AWG
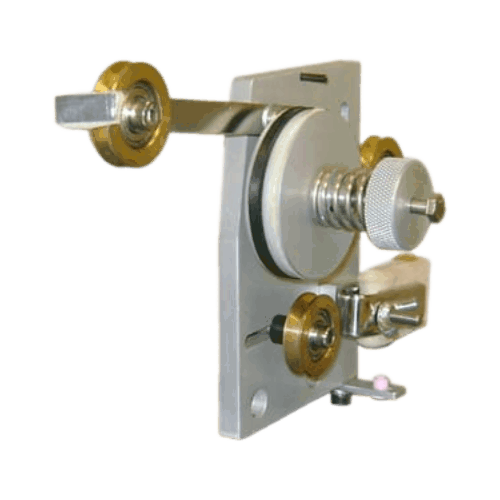
GSM-L01 – Tensioner Head 24-14AWG
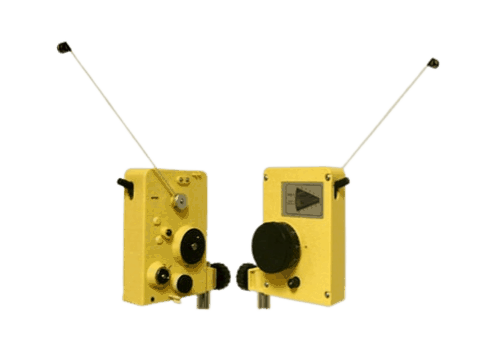
GSM-S01 – Tensioner Head 52-43AWG
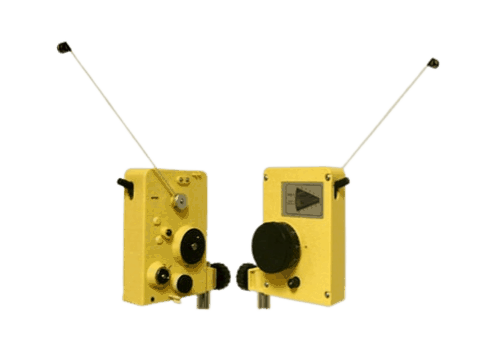
GSM-S02 – Tensioner Head 46-34AWG
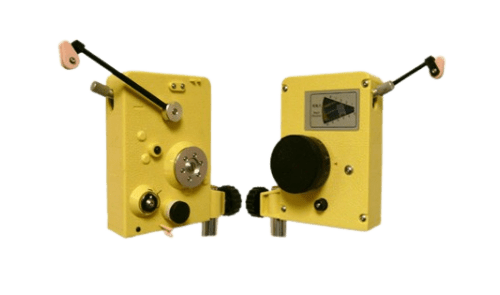
GSM-M01 – Tensioner Head 40-28AWG
Many More Models To Choose From
View All Products